How Computer Vision is used for Defect Detection and Quality analysis in Tyre Manufacturing
Computer vision is a powerful tool that can be used to improve defect detection and quality analysis in tyre manufacturing.
An automobile tyre is a crucial component of a vehicle as it is the only point of contact between the vehicle and the road. The tyre not only supports the weight of the vehicle but also plays an essential role in vehicle dynamics. It ensures a smooth ride by absorbing shocks and vibrations from the road. Any imperfections or defects in the tyre can significantly impact vehicle handling, stability, and safety. These minor issues can result in discomfort while driving, but in extreme cases, they can lead to severe accidents. Therefore, it is crucial to maintain and inspect tyres regularly to ensure optimal performance and safety.
A tyre is a complex structure made up of a combination of various materials, such as rubber, steel, and textiles. These materials have unique properties that directly impact the tyre’s performance. Although tyres are designed to be of high quality, hidden material defects can occur due to production errors or incorrect management systems. It is imperative that tyre manufacturers maintain consistent product quality on a small scale for their success. However, achieving this can be challenging, especially since many companies still rely on manual inspection methods, which can be time-consuming. Despite training, human inspectors are prone to making subjective judgments, which often results in maintaining an accuracy rate of only 90 to 95 per cent.
To address this challenge, automating and accelerating early defect detection can help tyre makers optimize production while reducing waste and overall costs. Early and accurate defect detection can also save human lives and preserve the reputation of the company. By using technology to detect defects, manufacturers can achieve a higher level of accuracy and efficiency in the production process. This technology can also provide insights into production efficiency and opportunities for improvement, allowing for a more streamlined and effective process overall.
Using artificial intelligence (AI) for quality control automation provides a more efficient and precise method of conducting visual inspections on production lines. This is a great way to ensure that the products meet high standards and that they are safe for the customers. Computer vision is a sub-field of AI that enables computers and systems to extract meaningful information from visual inputs, such as images and videos. With this technology, manufacturers can identify defects, measure product dimensions, and detect any other anomalies that could affect the quality of their products. Furthermore, by using AI for quality control, manufacturers can save on labour costs and reduce the risk of human error. The implementation of AI also brings a level of consistency and accuracy that is difficult to achieve with traditional manual inspections. Overall, the use of AI in quality control automation is a game-changer for manufacturers seeking to improve their production processes and deliver high-quality products to their customers.
AI Introduction
The Convolutional Neural network (CNN) is considered the most commonly used AI model for analyzing visual imagery. It is worth noting that in 2012, AlexNet demonstrated that deep learning can enable computers to perform intuitive tasks. This breakthrough proved to be a turning point in the development of AI models. Since then, CNNs have been adopted by every industry, from healthcare to agriculture, and have become an essential tool for businesses and organizations that rely on image recognition and analysis. For instance, CNNs are used in facial recognition technology to enhance security measures and in autonomous vehicles to detect and classify objects on the road. The versatility of CNNs has also led to their application in the field of entertainment, particularly in the creation of special effects in movies and video games.
CHISTATS APPROACH FOR ONE OF THE MAJOR TYRE MANUFACTURERS
In order to improve the performance of our model, we implemented a technique called pseudo-annotation. This method involves selecting a subset of the data and manually cropping out the unnecessary background or clutter from an image. For example, if there are people standing nearby, they would be removed, and only the defect region would be kept. Specifically, we sampled 20% of the images from each category and performed this pseudo-annotation process on them. The resulting cropped images were then added to our training dataset as new examples, effectively expanding the size and diversity of our dataset and improving the overall accuracy of our model.
Reducing the total number of classes and using pseudo annotation improved our model’s test accuracy. This was a natural outcome since the model could now focus more easily on the crucial features of the classes.
The Approach
Once the data has been split into training, validation, and test sets, the next step is to train a deep-learning model on the entire training dataset. After training the model, we evaluated its performance on the test set and observed a test accuracy of around 60%. However, to gain a deeper understanding of our model’s performance, we created a confusion matrix from our test results.
A confusion matrix is a table of numbers that indicates where a model makes mistakes. It displays the predictive performance of a classification model in a class-wise distribution. The confusion matrix maps the predictions to the original classes to which the data belong. Below is an example of a confusion matrix for a case with three classes: A, B, and C.
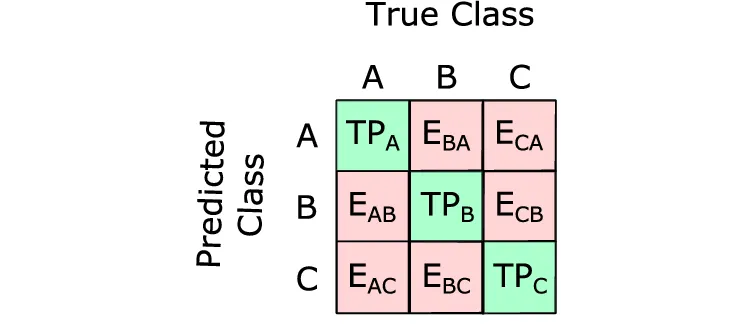
The green diagonal elements are called true positives, where the true class and the predicted class match.$$ E_{XY} = The \ true \ class \ was \ X, \ but \ the \ predicted \ class \ was \ Y$$
Failed to render LaTeX expression — no expression found
From the confusion matrix, we identified the set of classes that our model was confusing with one another.
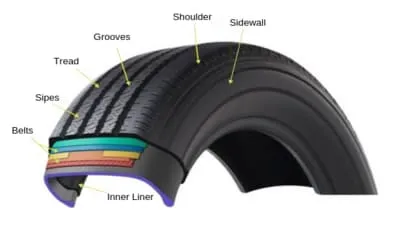
As we can see in the image above, the tread is the part of the tyre that makes contact with the road surface. One of the insights we gained from the confusion matrix was that our model had high confusion among the set of defects that were arising in the tread. And similar was the case with the different classes of defects that were present at the sidewall.
The challenge here was homogeneity- in some cases, both classes (good and defective) would have around 90% of the same features. Therefore, the goal is to accurately identify the 20% of the features that differ.
Due to the small percentage of recognizable features, it is challenging for a single model to classify a tyre image into many different classes correctly. Hence, we attempted to use model ensembling.
Ensemble models is a machine learning approach to combine multiple other models in the prediction process.
Final Approach
First, we merged some tyre defects into their respective parent categories and trained a first classifier (C1) that distinguishes tread-related defects from other types of defects.
If C1 predicts “Yes”, that means the defect is related to tread, and the next step is to forward the image to the classifier (C2) trained on tread-related defects.
If C1 indicates ‘No’, then the image is fed into C3, a classifier specifically trained to recognize side-wall-related defects as opposed to other types of defects.
We followed this approach until we merged all the similar-looking defects.
This was the training approach we settled on, and our overall accuracy was more than 90%.
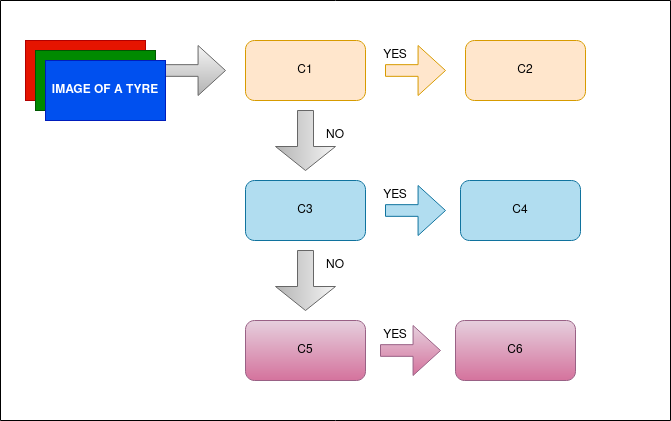
In conclusion, detecting and analysing defects in tyre manufacturing are crucial aspects of ensuring optimal vehicle performance and safety. While traditional manual inspection methods have limitations in terms of accuracy and efficiency, the use of artificial intelligence and computer vision technology has proven to be a game-changer. The implementation of AI for quality control automation not only provides a more efficient and precise method of conducting visual inspections on production lines but also brings a level of consistency and accuracy that is difficult to achieve with traditional manual inspections.
In addition, the use of AI can also provide insights into production efficiency and opportunities for improvement, allowing for a more streamlined and effective process overall. By adopting such innovative approaches, manufacturers can optimize production while reducing waste and overall costs, ultimately delivering high-quality products to their customers.
Want to talk with us? Have something you’d like us to cover? Drop your thoughts to sarang@chistats.com